后缩聚反应过程中因聚合物分子量不断增大,物料的特性 (如粘度,表面张力,流动性等 )变化极大,对分子扩散、气泡脱挥、气液界面传质产生很大影响。反应器内结构如园盘挡板配置对流型产生影响,盘片结构对成膜性、盘上和熔池中聚酯的交换和气液传质产生影响。为了促进生成的小分子 (水,EG,乙醛 )蒸发,园盘以一定的速度转动,使粘附其上的聚酯拉膜,不断更新表面,使水和 EG易于脱逸。不同聚合度的物料对成膜要求不同的转速范围,传质系数和膜面积与转速的关系,都需要定量的结果。
后缩聚反应过程的温度控制十分重要,反应温度过高,热降解反应增加,使产品端羧基指标不合格,过低的反应温度会达不到聚合度要求,工业上 (吉玛技术和钟纺技术 )这个温度范围相当狭窄,一般在 2 81~ 2 83℃ (指出口产品处 )。
终聚釜的压力控制是聚酯工业生产中最关键的控制点,通过出口物料的粘度 (或搅拌功率 )与压力组成的串级调节是保证产品质量 (特性粘度指标 )的基本手段,对民用聚酯产品,终聚釜的压力一般在 80~ 1 6 0 Pa范围内变化。
在后缩聚阶段,传质阻力成为总过程的主要阻力,提高传质推动力,即提高真空度是重要手段,但工业上大气量多级喷射泵产生的绝对压力的极限为 3 0 Pa左右,工业生产接近极限,所以提高传质系数和扩大传质面积是后缩聚反应过程的研究目标。
后缩聚反应过程是继预缩聚反应过程聚合物分子量进一步增大,与缩聚反应过程中发生的反应都相同,基于官能团等反应能力的简化,在后缩聚反应过程中主反应平衡常数,各种反应动力学、汽液平衡规律与预缩聚过程相同。区别主要在于气液传质速率和反应器内物料流动型式。
7.1.2 气液传质速率和传质面积
在后缩聚反应器中物料的平均聚合度从 1 4左右上升到 1 0 0左右,动力粘度从 480厘泊上升到 2 42 0 0 0厘泊,对气液传质速率影响极大。在高粘区要得到较高的气液传质速率,必须增加传质面积和传质系数,采用盘式或笼式搅拌装置能提供尽可能大的表面积,同时因拉膜造成了表面更新,提高了传质系数。内部搅拌装置的结构和转速对气液传质起关键作用。
7.1.3 后缩聚反应器的流动模型
后缩聚反应器的流动模型前人已作了很多研究,Ravindranath认为后缩聚反应器接近 PFR。 Lanbriet等人提出二相模型,液相作 PFR处理。Martin等人在二相模型的基础上提出动态模型。Amon等人的模型把熔体分为本体区的薄膜区。Yoon等人进一步引入本体与薄膜二区的混合。Yokoyama等人采用多级串联槽式模型来模拟后缩聚反应器。
本文根据冷模研究盘式后缩聚反应器接近于 PFR。采用 PFR可以减少返混,是最合理的反应器型式。在数学模型中的流动模型采用液相为 PFR,气相为全混的二相模型。
7.2 后缩聚反应过程数学模型
碳酸钙造粒机 http://jdl5.qqzyw.com/
高填充造粒机 http://hkb888.qqzyw.com/
滑石粉造粒机 http://hkb2.qqzyw.com/
色母粒造粒机 http://jdl8.qqzyw.com/
PVC电缆料造粒机 http://jdl6.qqzyw.com/
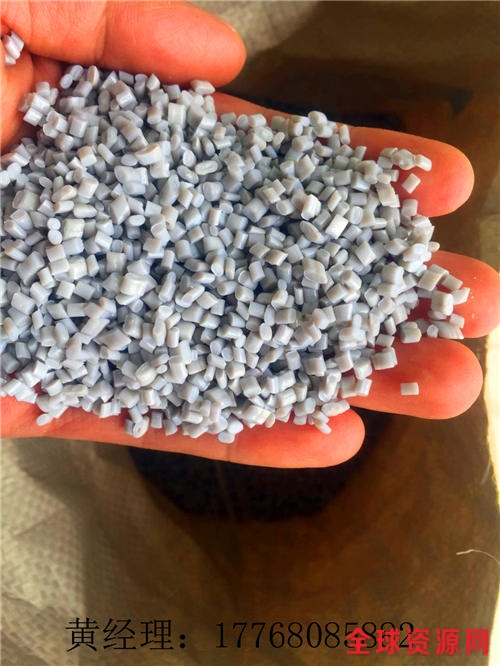
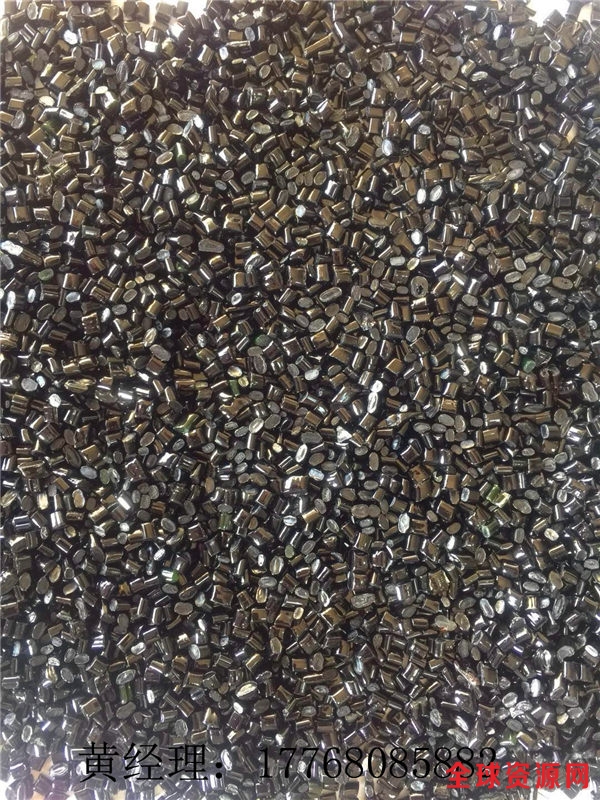
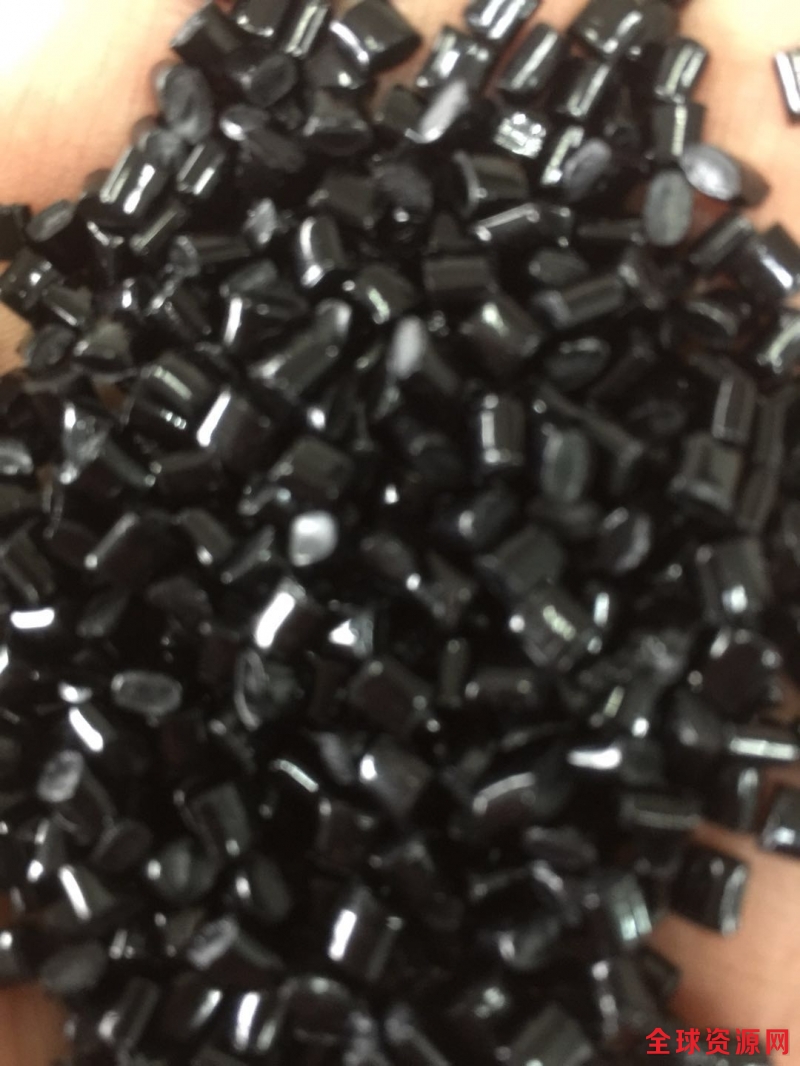
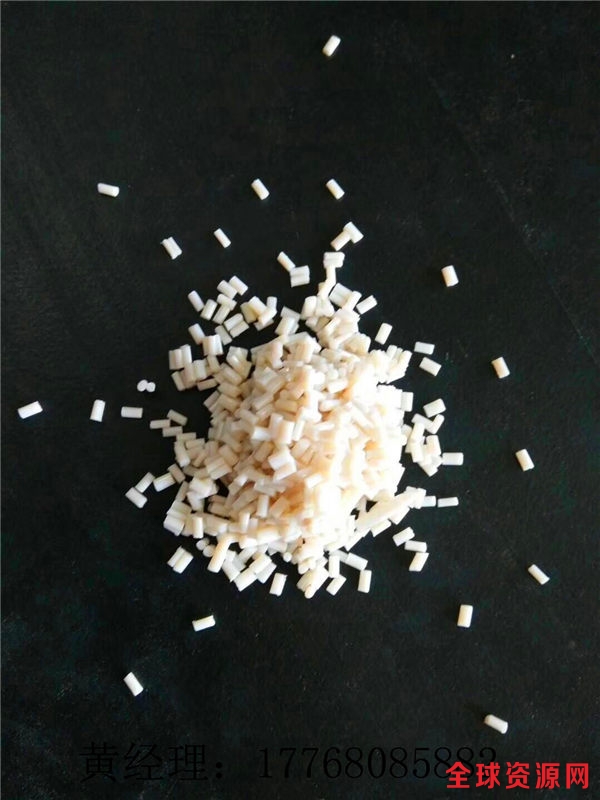